Cost-Benefit Analysis of 3D Printing Versus Traditional Injection Moulding Manufacturing
Financial Controller and Co-Founder of DustForge, Eric Liang discusses the cost benefits of 3D printing versus traditional manufacturing methods such as injection moulding. Selective Laser Sintering (SLS) 3D printing is emerging as a formidable alternative to traditional manufacturing methods like injection moulding. This article presents a cost-benefit analysis supporting SLS 3D printing by examining various aspects such as initial set-up costs, production flexibility, lead times, and material efficiency.
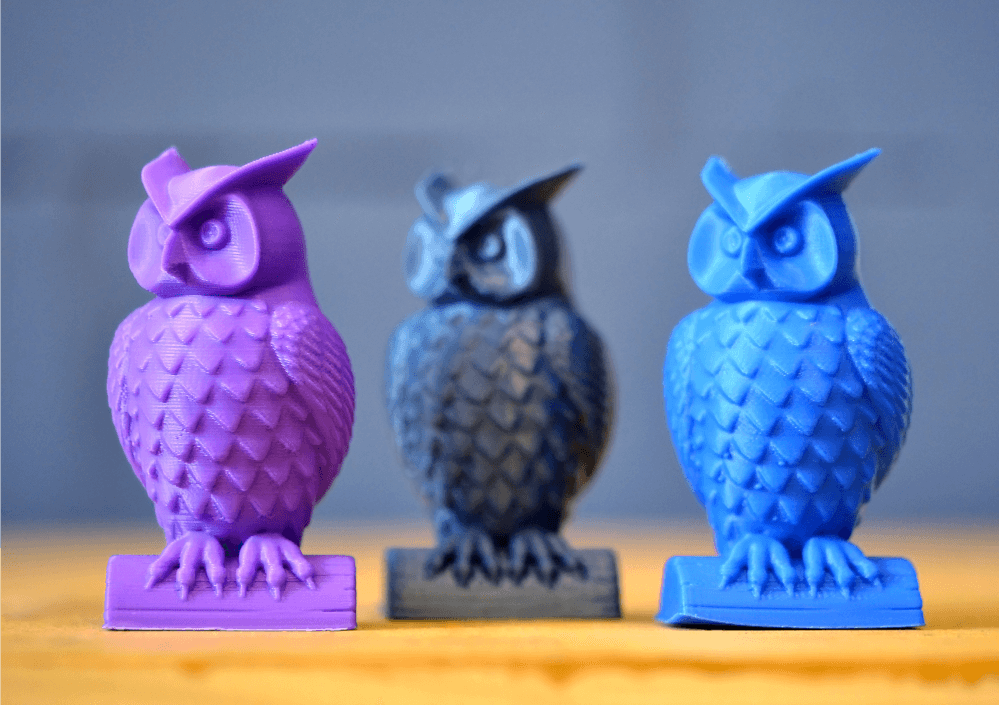
Initial Setup Costs
1. SLS 3D Printing:
Lower Tooling Costs: SLS does not require the creation of moulds or specific tooling. This significantly reduces the initial setup costs, making it especially advantageous for small to medium production runs.
Rapid Prototyping: The ability to produce prototypes quickly without extensive tooling investments means that companies can test and iterate designs more affordably.
2. Injection Moulding:
High Tooling Costs: Injection moulding requires the creation of custom moulds, which can be prohibitively expensive, particularly for complex designs and for low volume runs. These costs are typically justified only for large production volumes.
Fixed Costs: The high initial costs of moulds and set-up make injection moulding less cost-effective for small production runs or when frequent design changes are necessary.
Production Flexibility
1. SLS 3D Printing:
Design Complexity: SLS can easily produce complex geometries and intricate details that are difficult or impossible with injection moulding. This capability allows for greater innovation in product design.
Customisation: SLS is ideal for producing customised or one-off items. Each piece can be unique without incurring additional costs, making it perfect for bespoke products or personalised manufacturing.
2. Injection Moulding:
Design Limitations: Injection moulding is limited by mould design constraints, which can restrict the complexity of the parts produced. Design changes often require new moulds, adding to costs and lead times.
Mass Production: While excellent for high-volume production, injection moulding is not flexible when it comes to producing low quantities or customised items.
Lead Times
1. SLS 3D Printing:
Speed: SLS can significantly reduce lead times as it bypasses the need for mould creation. Once a design is finalised, production can begin almost immediately.
Rapid Iteration: The ability to quickly prototype and make adjustments allows for faster product development cycles, reducing the time to market.
2. Injection Moulding:
Longer Set-up Times: The process of creating moulds and setting up injection moulding equipment can take weeks or even months, leading to longer lead times.
Slower Iteration: Any design changes require new moulds, which delays the production process and increases costs.
Material Efficiency
1. SLS 3D Printing:
Material Utilisation: SLS is an additive manufacturing process, meaning material is added layer by layer only where needed. This approach minimises waste and maximises material efficiency.
Recyclability: DustForge uses TPM3D machines. 80% of unused powder can be recycled for future prints, further reducing material costs and waste.
2. Injection Moulding:
Material Waste: Injection moulding often results in material waste from sprues, runners, and excess material that must be trimmed off. While some of this can be recycled, it generally leads to higher material consumption.
Economies of Scale: Material costs per unit decrease significantly with higher production volumes, but this economy is not as beneficial for smaller runs.
Cost per Unit
1. SLS 3D Printing:
Consistent Costs: The cost per unit for SLS remains relatively stable regardless of the production volume, making it a cost-effective solution for low to medium production runs.
Short-Run Viability: For small batches, the per-unit cost of SLS is often lower than injection moulding due to the absence of tooling costs and shorter setup times.
2. Injection Moulding:
Economies of Scale: While the per-unit cost decreases significantly with higher production volumes, it remains high for small runs due to the amortisation of tooling costs.
High Initial Costs: The initial costs of moulds and setup make injection moulding economically viable only for large-scale production.
Conclusion
When comparing SLS 3D printing to traditional injection moulding, SLS stands out for its lower initial setup costs, greater production flexibility, shorter lead times, and efficient material usage. While injection moulding remains a powerful method for large-scale production, SLS offers significant cost advantages for small to medium runs, complex designs, and customised products. As technology advances and material costs decrease, SLS 3D printing is likely to become an increasingly attractive option for a wide range of manufacturing applications.