DustForge’s SLS Printing Process centered around quality
Selective Laser Sintering (SLS) is a powerful 3D printing technology employed by DustForge and renowned for its ability to create durable and intricate parts. As with any manufacturing process, quality control is crucial to ensure the final products meet the required standards. This article, written by Operations Director and Co-Founder of DustForge, Ryan Tan, delves into the SLS 3D printing production process, emphasising the critical steps involved in maintaining high-quality output.
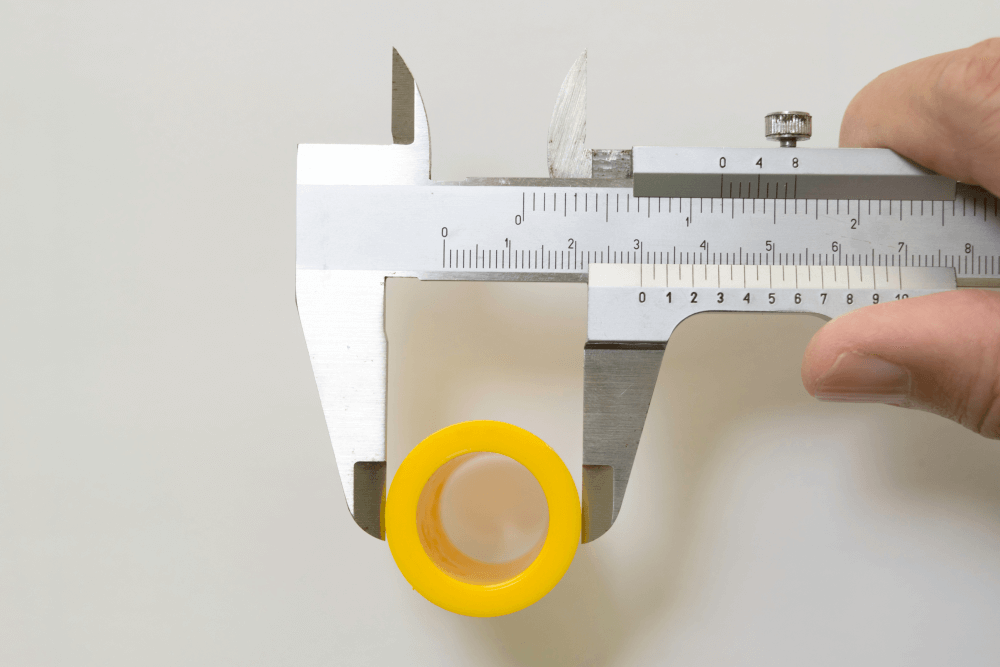
Understanding SLS 3D Printing
SLS 3D printing involves using a laser to sinter powdered material, typically nylon, layer by layer, to form a solid object. Unlike other 3D printing methods, SLS does not require support structures because the unsintered powder supports the part during printing. This capability makes SLS ideal for creating complex geometries and functional prototypes. DustForge has a proud history of using SLS and has a heritage in SLS machine manufacture (TPM3D).
The SLS Production Process
1. Design and Pre-Processing
CAD Design: The process begins with creating a detailed CAD model of the part. This model must be meticulously designed and optimised to maximise the capability of SLS to ensure accuracy in the final product.
File Preparation: The CAD file is converted into a format readable by the SLS printer, usually STL. The file is then sliced into thin layers, each representing a cross-section of the final part.
Material Selection: The choice of material is crucial as it affects the part's mechanical properties, surface finish, and functionality. Common materials include Nylon 12, Nylon 11, Polypropylene, TPU and various composites.
2. Printing
Setup: The SLS printer is prepared by loading the selected powder material and calibrating the laser.
Layering and Sintering: The printer spreads a thin layer of powder across the build platform. The laser then selectively sinters the powder based on the CAD design. This process is repeated layer by layer until the part is fully formed.
3. Post-Processing
Cooling: After printing, the build chamber must cool down to prevent thermal stress and deformation.
Depowdering: The printed parts are removed from the unsintered powder, which can be reclaimed and reused. This step involves using brushes, air blasts, and other tools to clean the parts thoroughly.
Finishing: Depending on the application, additional finishing processes such as tumbling, bead blasting, dyeing, or coating may be applied to enhance the part's appearance and properties.
Quality Control in SLS 3D Printing
Maintaining high quality in SLS 3D printing involves rigorous control measures throughout the production process:
1. Material Quality Control
Powder Consistency: Ensuring uniform particle size and distribution is essential for achieving consistent layer density and mechanical properties. Regular testing of the powder for contamination and degradation is crucial.
Storage Conditions: Proper storage of the powder material to avoid moisture absorption and contamination is vital. DustForge employ a controlled environment with regulated humidity and temperature to ensure powder injtegrity.
2. Process Monitoring
Laser Calibration: Regular calibration of the laser ensures precise energy delivery, which is critical for consistent sintering.
Environmental Control: Maintaining a stable environment within the build chamber, including temperature and humidity, helps prevent defects such as warping and uneven sintering.
3. Part Inspection
In-Process Monitoring: DustForge’s advanced SLS system includes in-situ monitoring technologies that track the build process in real-time, detecting anomalies that could affect part quality. This monitoring is performed remotely, 24 hours a day during production.
Post-Process Inspection: After printing, parts undergo various inspection techniques such as dimensional measurement, surface roughness testing, and non-destructive testing (e.g., X-ray or CT scanning) to ensure they meet the specified requirements.
4. Consistency and Repeatability
Statistical Process Control (SPC): Implementing SPC methods helps monitor process variability and maintain consistency across production runs.
Documentation and Traceability: Keeping detailed records of the production parameters and material batches ensures traceability and facilitates quality assurance.
Ensuring High Standards
To consistently produce high-quality SLS parts, DustForge has adopted a comprehensive approach to quality control. This involves continuous monitoring and improvement of all aspects of the production process, from material selection and machine calibration to post-processing and inspection. Investing in advanced quality control technologies and training personnel to recognise and address potential issues early in the process significantly enhances the reliability and performance of SLS 3D printed parts. By prioritising quality control, DustForge can leverage the full potential of SLS 3D printing to create superior products that meet the demanding standards of various industries.
Conclusion
SLS 3D printing offers remarkable capabilities for producing complex and high-performance parts. However, achieving consistent quality requires meticulous attention to every step of the production process. By implementing stringent quality control measures, DustForge ensures their SLS-printed parts are reliable, precise, and of the highest quality, thereby unlocking the full potential of this innovative technology.