Reengineering and Reimagining Existing Products Using 3D Printing
The advent of 3D printing has revolutionised most industries, providing innovative solutions for reengineering and reimagining existing products. This transformative technology offers significant advantages, from enhancing product design to streamlining production processes, making it a vital tool in modern advanced manufacturing.
Enhancing Product Design
One of the primary benefits of 3D printing in product reengineering is its ability to enhance design flexibility. Traditional manufacturing methods often impose design constraints due to tooling limitations and material restrictions. However, 3D printing enables designers to create complex geometries and intricate details that were previously impossible or too costly to produce. This capability allows for the optimisation of existing products, improving functionality and performance.
For example, in the aerospace industry, companies are using 3D printing to redesign aircraft components. By reengineering parts to be lighter and stronger, manufacturers can significantly improve fuel efficiency and reduce emissions. The ability to produce complex internal structures, such as lattice designs, results in parts that are both lightweight and robust, enhancing overall performance.
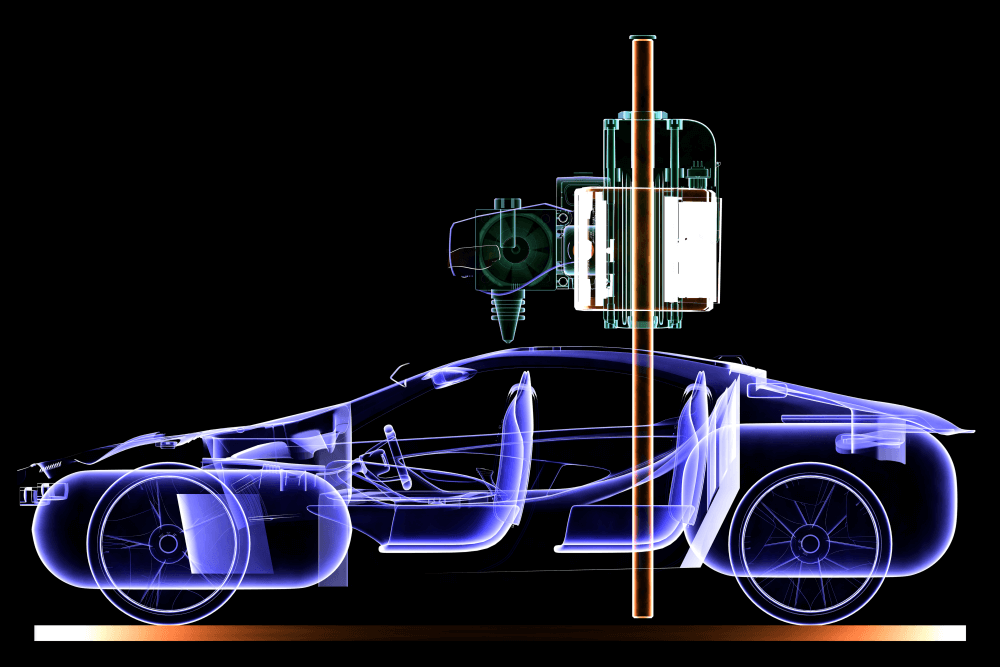
Streamlining Production Processes
3D printing also streamlines production processes, reducing lead times and costs. Traditional manufacturing
methods often involve multiple steps, including mould creation, machining, and assembly. These steps can be
time-consuming and expensive, especially for low-volume production runs. In contrast, 3D printing allows
for the direct creation of parts from digital designs, eliminating the need for intermediate steps and
reducing the time from concept to finished product.
In the automotive industry, manufacturers are leveraging 3D printing to produce custom parts and prototypes
quickly. This rapid prototyping capability enables engineers to test and iterate designs more efficiently,
accelerating the development cycle. Additionally, 3D printing can produce end-use parts on demand, reducing
the need for large inventories and enabling just-in-time manufacturing.
Mass Customisation and Personalisation
Another significant advantage of 3D printing is its ability to facilitate customisation and
personalisation. Traditional manufacturing methods are often geared towards mass production, making it
difficult and costly to produce custom or one-of-a-kind items. However, 3D printing allows for the
economical production of customised products, meeting the specific needs and preferences of individual
customers.
The healthcare industry has seen remarkable advancements in this area, with 3D printing being used to
create personalised medical devices and implants. Custom prosthetics and AFO’s, for example, can be
tailored to fit the unique anatomy of each patient, improving comfort and functionality. Additionally,
3D-printed surgical guides and models assist surgeons in planning and executing complex procedures with
greater precision.
Sustainability and Waste Reduction
Sustainability is becoming increasingly important in manufacturing, and 3D printing offers significant
environmental benefits. Traditional reductive manufacturing processes often result in substantial material
waste, as excess material is removed during machining or discarded during moulding. In contrast, 3D
printing is an additive process, building parts layer by layer with minimal waste. This efficiency not only
reduces material costs but also lessens the environmental impact of production.
Moreover, 3D printing enables the use of recycled and biodegradable materials, further contributing to
sustainability efforts. By reimagining products with a focus on eco-friendly materials and processes,
manufacturers can reduce their carbon footprint and promote a circular economy.
Case Studies and Success Stories
DustForge are presently assisting several companies to successfully reengineered and reimagined products using 3D printing, demonstrating the technology's transformative potential. For instance, an agricultural client employed 3D printing to redesign their fabricated sheet metal product range. This client has 1600 SKU’s that sell globally, but in relatively low volumes (10-900 p.a.) 3D printing has enabled them to print these products in plastic, adding significant design value, improving performance, reducing the product weight (hence distribution costs), reducing the BOM from 40+ components to 2, reducing labour by 95%, producing just-in-time, alleviating the need to costly stock on hand, and reducing the COGS on most SKU’s.
Conclusion
3D printing is reshaping the landscape of product development and manufacturing, offering unprecedented opportunities for reengineering and reimagining existing products. Its ability to enhance design flexibility, streamline production processes, enable customisation, and promote sustainability makes it an invaluable tool for modern industries. As technology continues to evolve, we can expect even more groundbreaking advancements and applications, further solidifying 3D printing's role in the future of manufacturing.